輔助自動化設備提升鈑金企業競爭力
文/李冰·深圳市銳特爾精密模具有限公司
隨著各行業產品同質化,競爭白熱化,人工不斷攀升的微利時代的到來,對于中小型企業,每一道工序,每一道工藝對企業控制成本,提高利潤率就顯得非常重要。特別是鈑金加工企業,模具是日常消耗品,對模具選擇和使用,以及正確的保養就尤其重要了。下文就鈑金加工中的重要環節數控沖輔助自動化設備對模具使用中的研(刃)磨問題展開一些實用性的討論。
目前在數控模具生產中國內只有極少數企業采用了先進、高效、高精密機床和自動化生產技術。由于數控模具的精密性,磨削加工工作量占模具總的制造工時的90%以上。而目前磨床加工工藝能實現數控化、自動化的企業就更加廖若星辰了!模具的質量與模具制造精度密切相關,特別是模具配合精度和表面粗糙度跟磨削有著密切關系,模具刀口的質量與磨削工藝就更加密切了,這就是很多鈑金企業普遍反映的一個問題:新模具刀口非常鋒利,也非常耐用,一旦客戶自己修磨刀口后,模具沖裁次數就不如新模具了,于是絕大多數客戶將問題歸結于模具質量不好。以筆者從事磨削工作二十多年的經驗來看,這跟磨削的工具、磨削的工藝、磨床的先進性有關,鈑金企業將自己研磨后的模具質量問題簡單的判定為模具廠是非常值得商榷的。 要提升數控沖切效率,要提高數控沖切品質,要減少去除數控沖切后的披鋒毛刺的工時,就必須要檢討導致模具失效的主要因素:⑴模具結構;⑵模具材料;⑶冷、熱加工的制造工藝(如鍛造、切削加工、熱處理、磨削加工、放電加工等);⑷模具工作條件等。要提高模具壽命,減少生產中的換模具的等待工時,就必須對導致模具損傷的原因及各種影響因素進行細致的分析,制定克服的辦法和措施。
磨削加工對模具壽命的影響目前仍然未引起業界的充分重視,由于不恰當的磨削工藝,造成工件表面燒傷退火、磨削后的龜裂、磨削粗糙及產生磨削應力,致使后續工序及模具在使用期間的機械疲勞產生的不耐磨,冷熱疲勞產生裂紋,將嚴重影響模具的使用壽命。研究和探討如何提高磨削加工質量,提高模具使用壽命、延長使用時間,促進行業采用模具制造和再研磨的新技術、新工藝,提高鈑金企業利潤率才是筆者的目的,本文就一些磨削及材料熱處理的基礎理論與大家探討。
模具的磨削加工原理及現狀
磨削過程的實質是工件被磨削了金屬表層,在無數磨粒瞬間的擠壓、磨擦作用下產生變形,而后轉為磨屑,并形成光潔表面的過程,磨削的全過程表現為力和熱的作用。
⑴在磨削過程中,加工表面在切削熱作用下產生熱膨脹,此時工件金屬基體溫度較高,因此表面產生熱壓應力。當磨削結束時,工件表面溫度降低,由于表面已產生熱態塑性變形并受到基體的限制,因此表面產生殘余拉應力,工件里層產生殘余壓應力。
⑵一般情況下的內外圓或者平面磨削時,砂輪與工件為弧線接觸,砂輪切削時工件產生塑性變形及砂輪與工件之間劇烈的摩擦阻力,從而在砂輪與工件間形成大小相等,方向相反的磨削力,同時由于表層材料塑性變形時使工件材料內部金屬分子之間產生相對位移,形成內摩擦而發熱,砂輪和工件之間外摩擦也產生熱量,這種磨削熱在磨削區會產生局部瞬時800~1000℃的高溫,而一般普通砂輪是不易傳熱的,所以80%的熱傳入工件和磨屑,而金屬在固態下隨溫度的改變,由一種晶格轉變為另一種晶格,發生金相組織的轉變。在磨削淬硬鋼時,冷卻充分,表面層產生二次淬火,部分殘余奧氏體轉變為馬氏體,而馬氏體比容較大,比容增加,表面產生壓應力;如果磨削冷卻不好,或不用冷卻液的干磨,表面產生回火,發生馬氏體轉變,表面產生拉應力(如γ-Fe轉變為α-Fe時鐵的體積會膨脹1%),這些應力(殘余應力可達到500~1000MPa),如果超過材料的屈服極限時,便產生磨削裂紋,另外如果熱處理淬火后模具未立即回火,淬火溫度過高,有網狀碳化,回火后未回火的馬氏體或殘余奧氏體過多,在磨削時都會產生相變,發生應力使工件表層產生裂紋。磨削裂紋是一種很細微的表面裂紋,磨削裂紋形態一般有3種:平行線條狀、網絡龜裂狀、八字形裂紋。裂紋的發生方向和模具形狀有關,裂紋的發展方向還和砂輪在工件表面磨削方向有關,其深度大約在0.03mm以內。
⑶磨削時:砂輪鈍化后不鋒利,人工進刀量大不均勻,冷卻不良等使工件表面產生的溫度達300℃以上,引起工件表面發生燒傷退火現象,這種現象在國內絕大多數的模具企業和鈑金企業再研磨時都普遍存在。主要與員工要趕工制造,跟計件工資以及廠家磨床設備陳舊、生產工藝落后、管理體系不健全等有關。
如何減少模具磨削加工缺陷
⑴ 正確的細分磨削工藝:粗磨、細磨、精磨、拋光等,合理選擇磨削用量,銳特爾公司采用數控磨床加工,徑向進給量自動控制,擯棄人為的大進給量,同時磨削工藝由電腦自動控制為:粗磨、細磨、精磨、拋光,同時根據磨削表面的大小來自動設定磨削進給量,進給時間和周期,磨削的全過程為較小的、均勻的、細致的進刀量。沒有數控磨床的情況下,如適當減少徑向進給量及砂輪速度、增大軸向進給量,使砂輪與工件接觸面積減少,散熱條件得到改善,也能有效地控制表層溫度的升高,從而提高模具品質。
⑵ 合理選擇和修整砂輪,一般廠家采用白剛玉的砂輪,它的性能硬而脆,且易產生新的切削刃,因 此切削力小,磨削熱較小,在粒度上使用中等粒度,如46~60目較好,在砂輪硬度上采用中軟和軟(ZR1、ZR2和R1、R2),即粗粒度、低硬度的砂輪,自銳性好可降低切削熱。精磨時選擇適當的砂輪十分重要,針對模具鋼材的高鉻、高釩、高鉬、高鎢狀況,選用GD單晶剛玉、大氣孔的砂輪比較適合(圖1),同時要經常修整砂輪,保持砂輪的鋒利性,防止磨削燒刀退火(圖2)及龜裂。
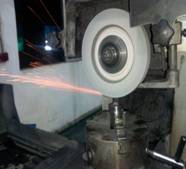
圖1 GD單晶剛玉粗粒度大氣孔砂輪與細粒度砂輪比 圖2 沖頭刀口平面磨床研磨時被燒刀退火的情況
⑶ 當加工硬質合金、淬火硬度高的材料時,優先采用有機粘結劑的金剛石砂輪,有機粘結劑砂輪自銳性好,磨出的工件粗糙度可達Ra0.2μm,CBN(立方氮化硼)砂輪加工效果更佳,當然是在數控成型磨床、坐標磨床、CNC內外圓磨床等高速、高精度機床上精加工,方能體現這種工藝的效果。在磨削加工中,要注意及時修整砂輪,保持砂輪的銳利,當砂輪鈍化后,會在工件表面滑擦、擠壓,造成工件表面燒傷,強度降低。因此選購數控磨床自動磨削,自動修整砂輪,自動控制進給就尤為重要了。
⑷ 合理使用冷卻潤滑液,發揮冷卻、洗滌、潤滑的三大作用,保持冷卻潤滑清潔,從而控制磨削熱在允許范圍內,以防止工件熱變形。改善磨削時的冷卻條件,如采用浸油砂輪、內冷卻砂輪、氣槽式砂輪等。將切削液引入砂輪的中心,切削液可直接進入磨削區,發揮有效的冷卻作用,防止工件表面燒傷、內應力的產生。數控磨床即采用這種砂輪及冷卻方式,對模具刀口刃磨(研磨)后使用壽命提高2~3倍。
⑸ 將模具熱處理后的淬火應力降低到最低限度,因為淬火應力、網狀碳化組織在磨削力的作用下,組織產生相變極易使工件產生裂紋,因此模具熱處理后必須超深冷處理。銳特爾模具超深冷處理為-150℃。
⑹ 對于高精度模具為了消除磨削的殘余應力,在磨削后還應進行低溫時效處理以提高韌性;消除磨削應力必須將模具再回火處理,這樣硬度可下降1HRC,殘留應力降低50%~65%。由于數控沖床模具需要快速交貨,一般廠家很難對加工好的模具再處理,只有大型模具廠家有可能做到這個工藝,因為大型模具廠家基本都是大規模做半成品或者成品庫存,常用規格模具可以做到加工完成后再做人工或者自然時效處理,這也是大廠同樣材質,同樣工藝制造,模具品質普遍比小廠好的重要原因之一。
⑺ 采用電解磨削加工,改善模具制造精度和表面質量。電解磨削時砂輪刮除模具表面的氧化膜,而不是磨削金屬,因而磨削力小,磨削熱也小,不會產生磨削毛刺、裂紋、燒傷等現象,一般表面粗糙度可優于Ra0.16μm;另外,砂輪的磨損小,如磨削硬質合金,碳化硅砂輪的磨損量大約為磨削掉的硬質合金重量的400%~600%,用電解磨削時,砂輪的磨損量只有硬質合金磨除量的50%~100%。
模具磨削的解決方案
⑴ 在模具制造時要充分重視磨削工序,嚴格控制磨削進刀量,充分水冷卻,及時修整砂輪,增加空刀磨削時間和次數,徹底消除磨削微裂紋,將殘余應力降低到最低限度,以提高模具的使用壽命;
⑵ 最根本的解決方案是購置數控磨床,將磨削工藝標準化、程序化、自動化,徹底消除人為的大進 刀、冷卻不充分、不及時修整砂輪的鈍磨削等,最終達到提高模具質量,延長模具使用壽命。
模具的刀口磨削(刃磨、研磨)
模具刀口的磨削原理和模具制造過程完全相同,下面就鈑金企業在模具使用中的研磨方法做簡略敘述:
數控自動研磨機與平面磨床研磨對比(圖3):
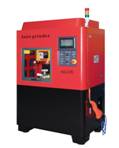  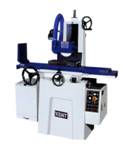 ⑴ 數控自動研磨機(圖4)不占人員、不需熟練磨工,磨削量、進給量、水冷卻、甚至機床潤滑等設定均由系統自動控制,操作極其簡單。平面磨床需要專門人員、需要熟練磨工,否則修洗砂輪隨意、進給量隨意、沖水隨意等研磨質量及安全問題將長期困擾客戶。
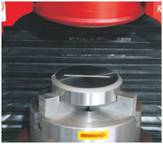
⑵ 數控自動研磨機安全、快捷、方便,特殊制作的高精度三爪自定心卡盤,厚塔AB沖頭不需拆卸彈簧即可研磨(圖5),不同規格的模具安裝方便;由于厚塔上模沖頭207mm比較長,平面磨床裝夾很不方便,而且容易出現A工位下模打飛或沖頭小刀口折斷等不安全事故,同時下模只有30mm又比較短,平面磨床需要長行程的升降磨頭,費力費時,影響磨削效率和研磨質量。
a) b) &, ;, ;nbs, p; c)
圖5 自動研磨機與平面磨床研磨沖頭時安裝對比
a)自動研磨機研磨厚塔AB工位模具可免拆彈簧即可研磨 ,沖頭不會被磁化;
b)平面磨床研磨沖頭需要拆卸彈簧打擊頭后才可以研磨沖頭,同時沖頭會被磁盤磁化,研磨后必須退磁,否則會導致沖孔時帶料。
⑶ 數控自動研磨機占地面積小,全罩式鈑金設計,防水無塵,可靠近數控沖床安裝,模具即鈍即磨,對于沒有備品的數控沖模,特別方便。平面磨床磨削有水霧和粉塵,不能靠近數控沖床擺放,磨削時產生的水霧和粉塵進入數控沖床滾珠絲桿和線性導軌會損害昂貴的機床設備。
⑷ 數控自動研磨效率高,自動研磨機3分鐘內就可以研磨好A、B沖頭,大刀口亦在數分鐘內完成;平面磨床卻需要30分鐘左右甚至更多時間。自動研磨機磨削后不需退磁工序,平面磨床研磨后必須退磁,否則沖壓時容易出現帶料現象,導致模具重復沖壓,打壞模具或者板材。
⑸ 數控自動研磨機磨削精度高,磨削屋頂式沖頭對稱性極佳,砂輪軸與工作面同軸設計,機床剛性和平行度一致,通過輔助工具可傾斜角度磨單斜(圖6)或者屋頂式沖頭;平面磨床磨削屋頂沖頭不方便,必須采用正玄磁盤或者其他專用工裝,磨削對稱度準確度不易控制,數控沖壓時容易出現偏載,導致模具破裂或者產品沖廢。
圖6 數控自動研磨機研磨剪切角(斜刃口)沖頭
圖7 平面磨床研磨沖頭剪切角(斜刃口)時,需要安裝正弦磁盤,通過人工打表找正方可實現研磨,同時研磨后必須要退磁,否則被磁化的沖頭在數控沖孔時會帶料。
⑹ 數控自動研磨機磨削品質高,采用氣槽式CBN砂輪,無需修洗砂輪,無火花磨削,對模具無人為損傷。CBN砂輪磨削時瞬間產生的溫度才280℃左右,模具刃口既無高溫火花退火又減小了加工應力,模具品質容易保證、耐磨性也相應提高了。平面磨床采用傳統鋼玉類砂輪磨削,需要修洗砂輪產生粉塵,磨削時模具刀刃表面會有大量火花產生,在熟練磨工操控及正常進刀量下傳統剛玉砂輪磨削工件時瞬間產生的溫度達800~1000℃高溫,事實上模具刃口相當于被局部退火或回火了、并再次產生了加工應力。實際加工中工人為了完成生產任務,人為的加大進刀量(圖8)和無水干磨(圖9)所產生更高的溫度,導致模具刀口表面退火卻又不易監控,在后續使用中會發現模具不耐磨,模具刃磨自然次數就增加了,模具使用壽命和數控沖床的加工效率大幅降低了。
圖8 進刀量過大,燒刀后退火,模具壽命減少 圖9冷卻液不足,也會導致燒刀 圖10正常研磨
結束語
總之模具在制造以及使用過程中要充分重視磨削工序,使磨削微裂紋和殘余應力降低到最低限度,以提高模具的使用壽命。模具的使用是模具設計和制造的延續,是驗證設計正確性的過程。在現代鈑金生產中采用了先進、高效、高精密機床和自動化生產技術,只有合理的使用模具,才能充分發揮先進數控沖床的性能,提高數控沖床的沖切效率,提高數控沖床的沖切品質,從而降低加工成本。也只有重視先進設備、配置先進模具、應用先進工藝,在使用過程中的規范化、標準化、自動化的鈑金企業,才能在日趨激烈的市場中贏得市場份額,才能持續經營和發展。
更多鈑金資訊,請掃描下方二維碼關注鈑金智造聯慧微信公眾平臺。
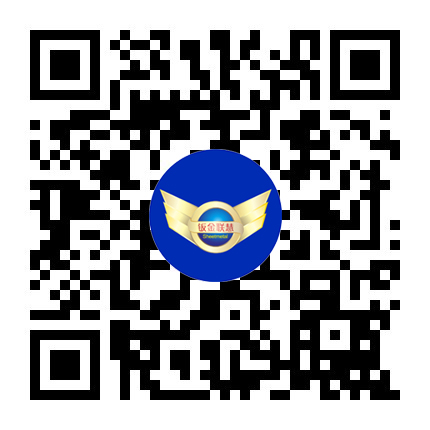
|